Machine Learning For Manufacturing Industry
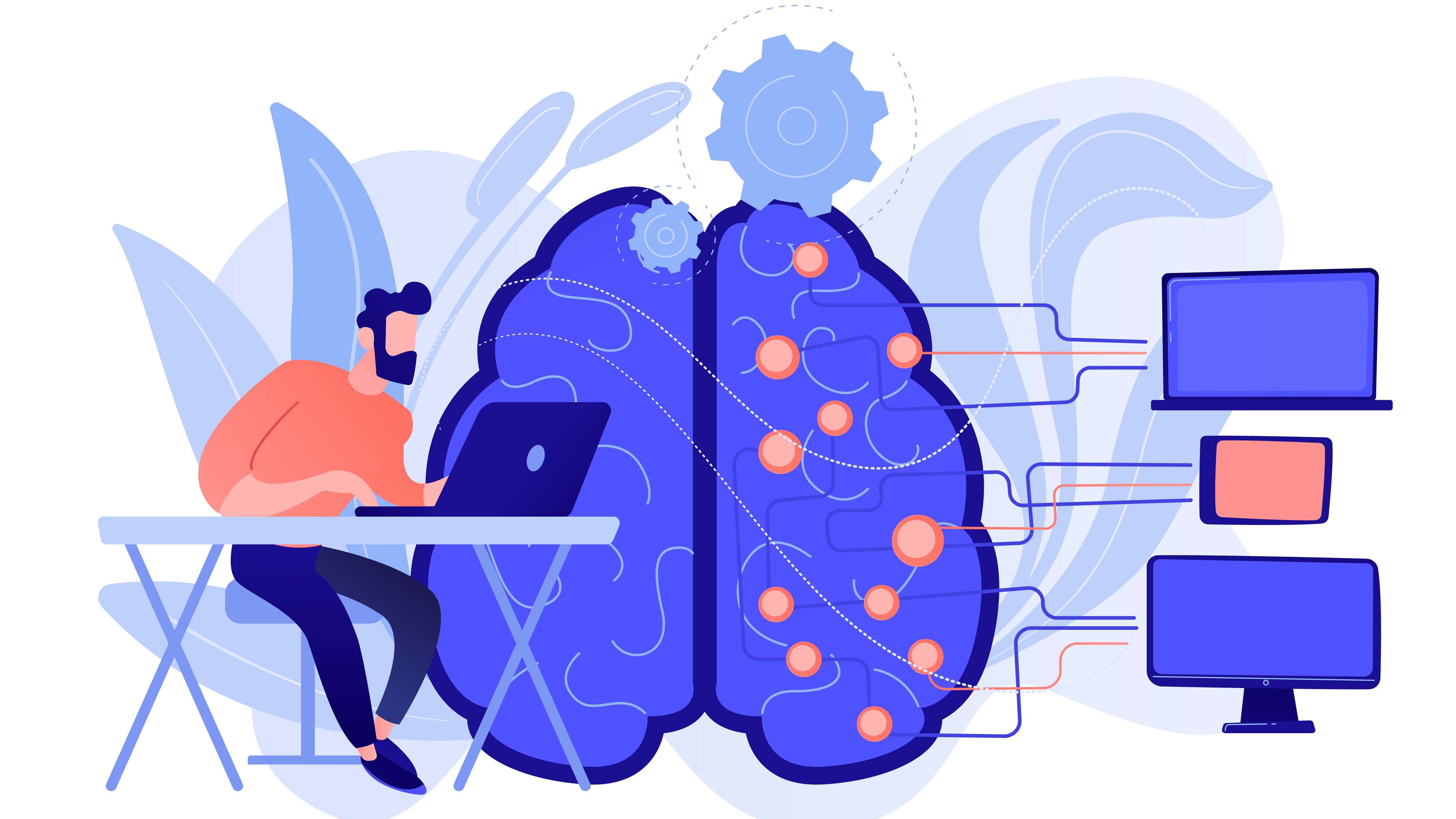
Machine learning is a branch of artificial intelligence that allows computers to learn without being explicitly programmed. It can be used to make predictions and decisions based on historical data, which makes it useful for many industries including manufacturing. The main goal of machine learning is to build systems that are able to perform tasks automatically or semi-automatically by using past experience and patterns found within the dataset. In this article we will discuss how machine learning can benefit your business in terms of improving quality control, increasing efficiency, reducing costs, and more. We’ll also provide an overview of what you need to know about machine learning before getting started with implementing it into your company.
What is Machine Learning ?
Before diving deeper into why machine learning is important for manufacturers, let’s take some time to understand exactly what it is. According to Wikipedia: “Artificial Intelligence, sometimes called machine intelligence, refers to computer programs designed to mimic human thought processes… AI has been defined as any intelligent agent capable of perceiving its environment and taking actions that maximize its chances of success at achieving goals specified by itself or others.” This definition includes all types of machines from robots to self-driving cars. As far as humans go, they have the ability to think logically and process information quickly. Machines do not necessarily possess these abilities but instead rely on algorithms to accomplish their functions. These algorithms may be written manually or created through machine learning techniques.
What Data are Manufacturers Collecting?
Manufacturing data sources – including business transactions, maintenance records, geographical data, and RFID scans – can all provide insights into industrial operations, in addition to the obvious ones such as sensors and PLCs. Of course, access to such data is required in order to extract those insights.
Industrial data is frequently siloed, which means it is only accessible by one department or division and otherwise isolated from the rest of the business, limiting its utility. According to some estimates, more than two-thirds of all industrial data gathered is wasted. This so called “black data,” which is frequently stored solely for compliance purposes, incurs storage expenses for manufacturers while providing no corresponding benefit.
Breaking down data silos in order to recuperate costs and get a higher ROI is a well known issue that has created a slew of manufacturing data visibility and data governance solutions.
Given the difficulty of manufacturing data management, one can question whether the costs of equipment, data collecting, and industrial data storage are truly worthwhile.
Maximizing the Value of Manufacturing Data
The path to digitalization in manufacturing may appear straightforward: capture more production data using a combination of legacy equipment instrumentation and industrial connectivity, then use that data with sophisticated manufacturing analytics.
Add to that the huge number of manufacturing AI applications in Industry 4.0, and it is easy to conclude that the most difficult problem in generating value from manufacturing data is determining where to begin. Unfortunately, it has been repeatedly demonstrated that the majority of digital transformations fail at the proof-of-concept stage, with a success rate of less than one in three.
This lack of employee involvement can be attributed to a variety of factors, including ineffective communication tactics.Finally, the key to extracting value from manufacturing data is to have a clear knowledge about the problem you’re attempting to solve and how methods like machine learning may help you solve it.
Machine learning, when used correctly, can help manufacturers attain new levels of product quality; but, they must first comprehend machine learning.
Machine Learning types for Manufacturing
To tackle challenges, machine learning employs a range of algorithms. These algorithms are usually classified based on how they learn. An algorithm’s learning style is determined by how it consumes data and whether that data is labelled or unlabeled. Unlabeled data does not have a tag or categorization, but labelled data does.
Consider units that have passed or failed an end-of- line test: if such units are identified as passing or failing in the data, the data set is labelled. If there is no indication of which sections passed or failed in the units, the data set is unlabeled.
- Algorithms that use labelled data are referred to as supervised learning algorithms.
- Algorithms that use unlabeled data are referred to as unsupervised learning algorithms.
- Algorithms that use partially labelled data are referred to as semi-supervised learning algorithms.
Which machine learning technique works best will be determined by the available manufacturing data and the situation at hand. As a result, manufacturers may decide that a combination of supervised, unsupervised, and semi-supervised learning across facilities, or even between lines within a single facility, is preferable.
Benefits of Machine Learning for Manufacturing
Machine Learning is changing the way industries like manufacturing work by making them more efficient. Following are the key benefits of machine learning for manufacturing by making them more efficient.
- Increasing manufacturing capacity by up to 20% while reducing material usage by 4%.
- More relevant data is being provided so that finance, operations, and supply chain teams may better manage factory and demand-side limitations.
- Improving preventative maintenance and Maintenance, Repair, and Overhaul (MRO) performance through higher prediction accuracy at the component and part levels.
- Providing manufacturers with the scale to control Overall Equipment Effectiveness (OEE) at the plant level, raising OEE performance from 65 percent to 85 percent.
- Machine learning is transforming relationship intelligence, and Salesforce is swiftly establishing itself as the market leader.
- Machine learning algorithms that evaluate which elements have the most and least impact on company-wide quality are revolutionising product and service quality.
- Machine learning is already increasing manufacturing yields by optimising team, machine, supplier, and customer needs.
- Machine learning will enable subscription models for production services, making the idea of Manufacturing-as-a-Service a reality.
- Machine learning is ideal for improving supply chains and increasing economies of scale.
- Machine learning will make it normal to know the exact price to charge a certain consumer at the right time to maximise margin and close sales.
Conclusion
Any company involved in Manufacturing has the opportunity to integrate machine learning into their operations and obtain a competitive advantage by gaining predictive insights into production.
The underlying technologies of machine learning are ideally suited to the complex difficulties that manufacturers face on a regular basis. Machine learning algorithms have the potential to improve prediction accuracy at every stage of manufacturing, from keeping supply chains running effectively to producing customised, built-to-order items on time. Many of the algorithms being created are iterative, with the goal of constantly learning and optimising outcomes. These algorithms iterate in milliseconds, allowing producers to seek optimal results in minutes rather than months.